Asbestos roofs offered excellent thermal insulation and impressive fire-retardant properties. However, the health hazards associated with asbestos led to its prohibition in the 1980s and 1990s. Consequently, metal profile sheets emerged as the preferred roofing material.
Metal profile roofs typically boast a lifespan of 40 to 70 years, contingent upon regular maintenance. Now, as we surpass the 40-year mark from developments in the 1990s, it's evident that roof degradation and defects are on the rise. These remediation projects typically involve addressing cut-edge corrosion issues and recoating the entire roof with a silicone system. In some cases, the corrosion has deteriorated the roof sheets to such an extent that an entire roof replacement is necessary.
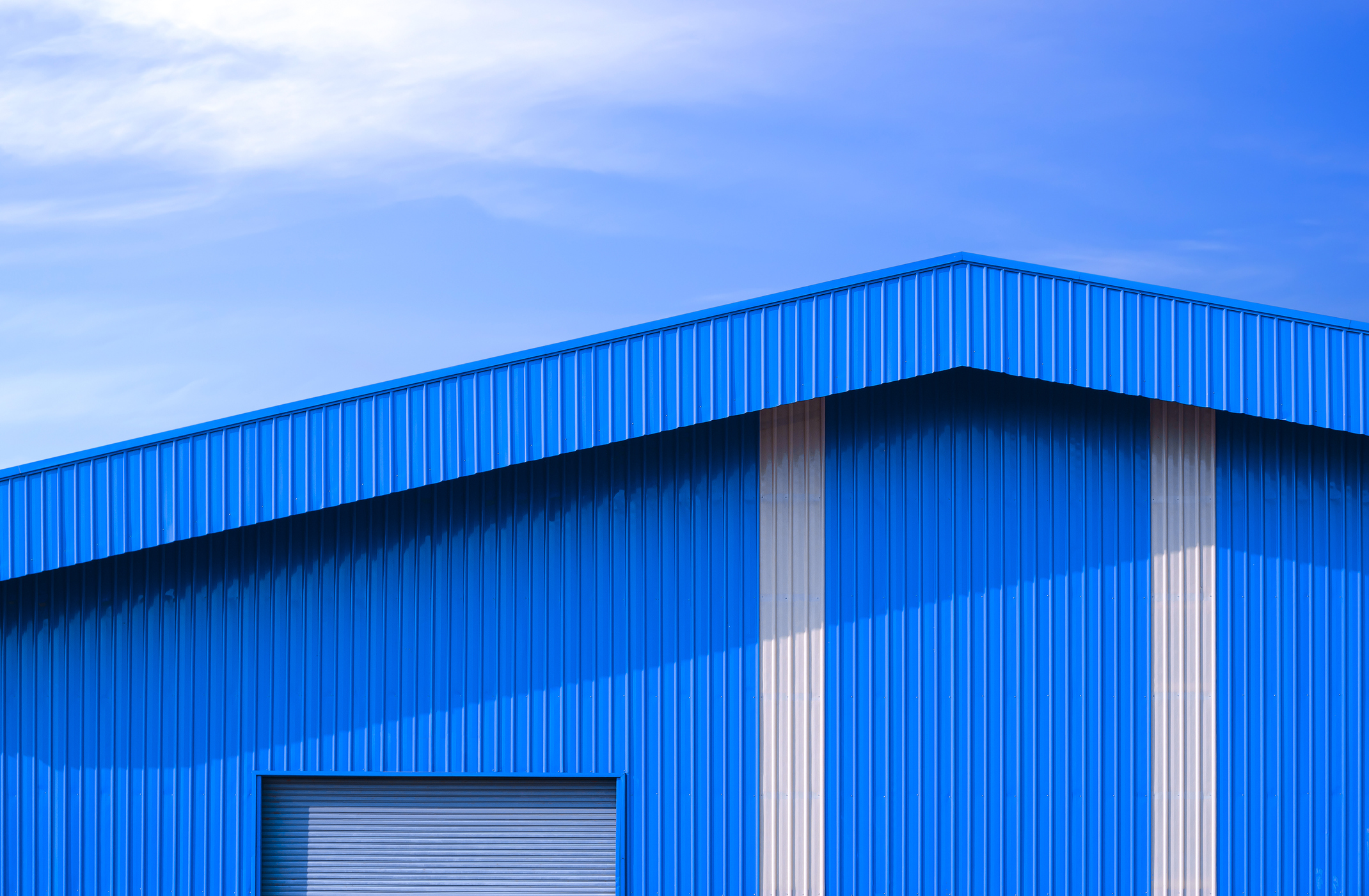
Solutions
To tackle this issue, it's crucial to conduct regular roof inspections and promptly address signs of cut-edge corrosion. There are available systems that allow for the complete coating of the roof, extending its life cycle by up to 25 years.
Costs
Replacing a roof is considerably more expensive than repairs, costing between £130-£150m² versus £42-£48m² for repairs. This cost differential can impact the decision-making process for property owners and managers, especially when considering budget constraints.
Sustainability
Sustainability considerations also play a vital role, as landlords increasingly focus on the embodied carbon impact of their decisions. In evaluating the environmental impact of different roofing solutions, the embodied carbon of roofing materials emerges as a critical factor.
A comparison between a metal profile built-up system replacement and a silicone coating reveals a substantial difference in their carbon footprint. The former stands at 12.9kg of CO2 per m², while the latter drastically reduces this to 2.4kg CO2 per m².
Matt Bishop from HD Sharmans, a manufacturer specialising in silicone coating systems, highlighted the significant environmental advantage of coatings over replacements. He emphasised -
Refurbishing a roof with coatings could effectively extend its life span, allowing for up to five refurbishments equivalent to a 125-year life span.
Bishop's calculations, considering the anticipated 16 million m² per year of roofs in the UK needing recoating, indicate a potential saving of 168,000 tonnes of carbon emissions compared to roof replacements. This reduction is equivalent to removing 80,000 cars from UK roads annually or heating over 62,000 homes for a year. These figures underscore the substantial environmental benefit and carbon emission reduction associated with opting for recoating over full roof replacements.
Conclusion
I anticipate seeing a growing number of projects opting for a full roof replacements in lieu of repairs - however, provided issues are caught early a robust repair strategy is the most cost, carbon and programme effective. While most of these properties operate under Full Repairing and Insuring (FRI) leases, with repair responsibility lying with the tenant, landlords have the option to trigger repairing obligations within the lease. They can also initiate interim dilapidations schedules to compel tenants to address roof issues before they deteriorate beyond repair.